Solving Valve Leaks for Space Exploration
Valves play a pivotal role in space exploration, controlling the flow of fluids and gases within spacecraft and other orbital systems. These components are essential for managing life-support systems, propulsion, and cryogenic fluid handling. However, they also pose significant challenges, as any malfunction or leak can lead to dire consequences.
The Apollo 13 mission is a sobering example: a faulty valve in the oxygen tank system contributed to the explosion that nearly ended in disaster. Similarly, the SpaceX Dragon explosion in 2019, where a faulty valve in the propulsion of the spacecraft system led to a catastrophic leak of propellant during a ground test. A single leak in a valve can result in the loss of critical fluids or gases, jeopardizing a spacecraft's operation and the lives of its crew. Addressing these vulnerabilities is vital, as the stakes in space are immeasurably higher than on Earth.
Engineers have employed numerous testing protocols, simulating extreme conditions, rigorous temperature fluctuations, and even testing in vacuum chambers to validate valve reliability. The consideration of advances in material science, such as the use of corrosion-resistant and temperature-resistant alloys, polymers, and packaging, has significantly improved reliability. However, the traditional valve still has one fatal flaw: a dynamic valve stem that pierces the pressure boundary of the valve, leading to atmospheric pressure. Many attempts to monitor leaks at these potential leak paths have helped identify the problem, but sometimes it is too late.
Despite these advancements, the complexity of the valve systems continues to present a significant challenge and is often seen as the chink in the armor. But what if that opening, that wound, that dynamic seal that requires packing to squeeze around a valve stem could be removed entirely? That is where magnetic valve actuation can completely eliminate the potential flow path to the outside world, allowing for a hermetically sealed valve. Through a magnetic coupling, a valve can be actuated through the solid wall of the valve body, resulting in no leak path (or wound).
The Reality of "Closed-Loop Systems” in Space
Piping systems are often thought of as "closed-loop systems" to ensure resource conservation and operational efficiency. Flanges will be welded together to eliminate even static seals. However, the term ‘closed-loop’ can be misleading, as traditional valves often leak into the atmosphere through their valve stems. This is especially true under extreme temperatures and pressures and with the handling of fluids, including liquid hydrogen or helium.
The valve stem is a dynamic seal that organizations rely on even though they have welded the rest of the system closed. Anyone that is familiar with a cryogenic processing plant has seen valves encased in a block of ice around the valve stem where super-chilled liquid escapes to the atmosphere. On Earth, leaking systems, though not ideal, can be addressed by refilling tanks; in comparison to space, it seems as simple as ‘just back the truck up and refill the liquid helium tank.’ This is not a luxury that is possible in the vacuum of space. This underscores the need for technological advancements that can eliminate leakage entirely.
Magnetic actuation offers a groundbreaking solution by entirely removing the leak path. The process fluid is completely isolated from the atmosphere, creating a truly closed-loop system that is hermetically welded in place with zero static seals or packing to rely on in many cases. Designs of ‘closed loop’ cryogenic systems in the vacuum of space have a fatal flaw if they rely on traditional externally actuated valves that allow for leaking past the valve stem to the atmosphere. Consider this: what might be possible now if standard valves leaked 0.000 parts per million into the atmosphere?
Revolutionizing Valve Technology for Space
Magnetic actuation technology exemplifies innovation in addressing valve leakage. Initially developed while working on the Morpheus II planetary lander project, a MagDrive actuated valve was hermetically sealed and designed to handle liquid helium at extremely cold temperatures. Liquid helium is notoriously challenging to manage due to its low viscosity and high volatility. The liquid helium in the process line was below the extreme cryogenic temperature of -269°C (or -452°F), pressurized to 3500 PSI, and moving through the valve at supersonic speeds in an atmospheric vacuum. This is an ideal recipe for a leaking valve stem, which is considered one of the hardest things to seal, especially when applying a standard valve that relies on packing.
The initial attempts to seal this challenge utilized a 6-foot standoff with various packing to seal a ¼” needle valve. The motor required to actuate this valve was oversized and had large power requirements just to overcome the stiction of the still leaking packing. When magnetic actuation was applied, the valve was hermetically sealed, and the emissions dropped to zero atmospheric leaks. This marked a significant breakthrough in valve technology.
By employing magnetic actuation, the design eliminates the traditional stem seal, which is the primary source of leaks. This development not only eliminated the leak path to the atmosphere but also reduced the size of the valve since the 6-foot offset was no longer needed to isolate the packing from the extremely cold temperature. With the elimination of the packing, one other discovery was made: the power requirements to actuate the valve dropped significantly. There was no longer a stiction between the valve stem and the packing, which had to be overcome with massive amounts of torque delivered to the stem. MagDrive’s ability to maintain hermetic sealing under such extreme conditions demonstrates its potential to transform fluid control systems for space travel and across various industries.
Down to Earth
The success of magnetic actuation in containing cryogenic fluids for space applications has inspired broader uses in industries such as oil and gas, chemical processing, methane, and hydrogen. These sectors often face similar challenges, complex fluids to manage with high pressures, extreme temperatures, and the need to prevent emissions. This has not been a new topic of discussion for these challenges, but they continue to be essential.
The United Nations Framework Convention on Climate Change met in Paris for COP21, and this was the first time we saw 196 countries unite in an international treaty to combat climate change. Still, it all depends on the countries’ efforts and commitments to reduce emissions for the overall impact. During COP27, the United States launched the “Net-Zer Government” initiative, which 18 other countries have joined.
These complex challenges and more generically called Fugitive Emissions, as anything that is escaping when not designed to allow the escape is a fugitive. Reducing fugitive emissions has become a high-priority goal for virtually every industry on Earth. With the added pressure on the environment, now the demands of investors and stakeholders on engagement in environmental improvements have been very much at the forefront of many decisions being made.
Over the past few years, corporate initiatives have been increasingly focused on eliminating these unintended releases. With nearly 50%+ of fugitive emissions coming from valves, a significant amount of a facility's fugitive emissions can be eliminated by installing magnetic actuation. Every pound or kilogram of product that escapes is money lost, including the raw material cost and the time, energy, and resources already expended to produce the product. Less obvious are the increased maintenance and operating costs associated with poorly performing leak detection programs. Notwithstanding those costs and in addition to the direct benefits of reduced emissions to the environment, there are financial benefits to the operating companies, too.
By adapting the technology originally envisioned for space, magnetic actuation offers a solution that eliminates leakage, enhances system reliability, and reduces environmental impact. Over the last year, magnetic actuation has been applied to multiple facilities, eliminating the fugitive emissions, which would have usually been released into the atmosphere, even with the best low-emission technology on the market. Magnetically actuated valves can mitigate the risks associated with leaks and emissions, ensuring more sustainable practices. The transition of this space-age technology to on-the-ground industries highlights the profound impact that this innovation, initially designed for space, may have on the planet.
This article was originally published in Valve World Magazine. You can view it HERE.
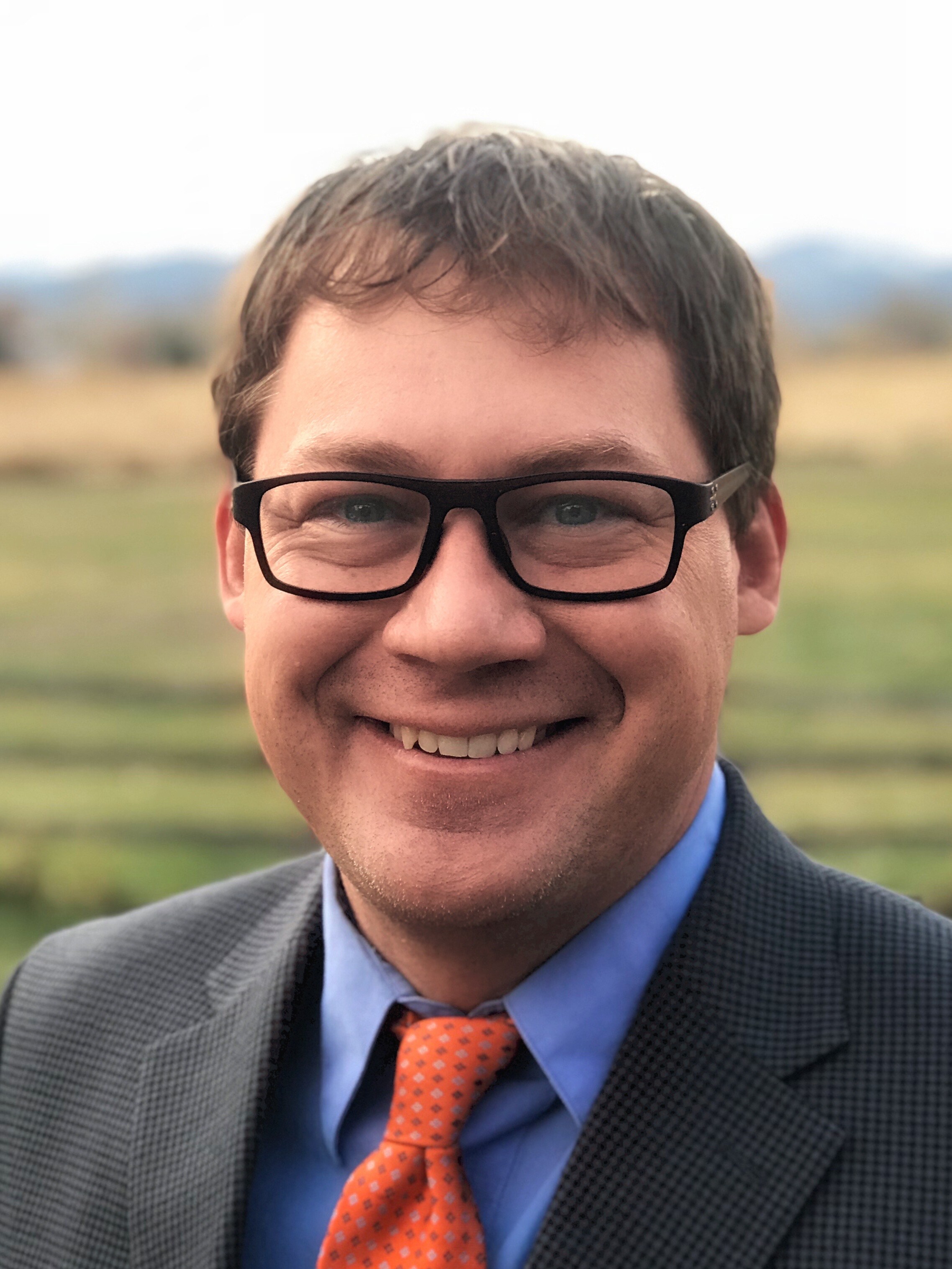
-1.jpeg)